Dust explosions have been linked to numerous fatal accidents in the United States. Between 1980 and 2012, the U.S. Chemical Safety Board investigated more than 280 combustible dust incidents that killed 141 people and injured 767 others.
Food manufacturing plants are among the most susceptible to these incidents, especially those in the baking segment that use a lot of flour and sugar. Of course, protecting your facility and employees is paramount, but the risk factors aren’t always obvious. Before we look at how to proactively protect your facility, let’s examine how these disasters can happen.
How does dust explode?
Combustible dust is a risk factor in the manufacturing of numerous food product segments, such as:
- Confectionary
- Bakery
- Cookie and cracker
- Snack food
- Blends/mixes
- Cereal
- Spices
These products contain ingredients that must be considered for their risk potential:
- Flour
- Spices
- Starch
- Sugar
Under the right conditions, table sugar can be as flammable as wood (which is made of cellulose, or lots of sugar molecules linked together). These dust particles are much more flammable because of their surface area-to-volume ratio.
According to the National Fire Protection Association (NFPA), a room with at least 5 percent of its surface area covered with more than 1/32nd of an inch of organic dust presents an explosion hazard. That thin layer of dust in a closed room is enough to trigger an explosion if the dust becomes airborne and is ignited.
Potential ignition sources include:
- Sparks from electrical or mechanical processes
- Open flames
- Electrostatic discharge (ESD)
Plus, just because a work area looks clean, that doesn’t necessarily mean it’s safe. Combustible dust can accumulate inside equipment and it can settle in hidden spaces like air ducts.
The 5 Elements of a Dust Explosion
Five elements are necessary to trigger a dust explosion. This combination is often referred to as the “Dust Explosion Pentagon.”
The first three elements are those needed for a fire, and the second two elements must be present for an explosion:
- Combustible dust (fuel)
- Ignition source (heat)
- Oxygen in air (oxidizer)
- Dispersion of dust particles in sufficient quantity and concentration
- Confinement of the dust cloud
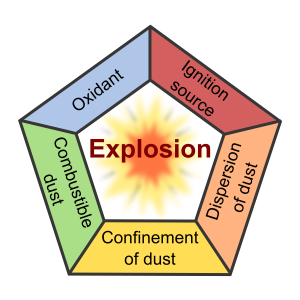
Dust explosions are particularly dangerous, because they often trigger a domino effect. An initial dust explosion in processing equipment may shake loose accumulated dust or may damage a containment system (such as a duct, vessel or collector). This causes more dust to become airborne and could trigger secondary explosions if ignited. These secondary explosions are often more destructive due to the increased quantity and concentration of flammable dust.
Preventing a Combustible Dust Explosion
These explosions are obviously a major risk for your employees and the structural safety of your facility, so how do you avoid them? The Occupational Safety and Health Administration (OSHA) and the NFPA recommend several steps to maintain work environments that are not conducive to dust explosions.
Dust Control
First, ensure you control the travel and amount of dust in your facility by:
- Implementing a program for hazardous dust inspection, testing, housekeeping and control
- Using proper filters and collection systems
- Minimizing the escape of dust from equipment and ventilation systems
- Using surfaces that are easy to clean and that don’t easily accumulate dust
- Inspecting for dust residue in hidden and open areas regularly
- Using cleaning methods that don’t generate dust clouds if ignition sources are present
- Using specialized vacuum cleaners that are approved for dust collection
- Locating relief valves away from dust deposits
By managing dust collection, you minimize the available “fuel” for potential explosions.
Ignition Control
Even if some dust is present, you can’t have an explosion without something to ignite it. Control ignition sources within your plant by:
- Using appropriate electrical equipment and wiring methods
- Controlling static electricity, including bonding of equipment to ground
- Controlling smoking, open flames and sparks
- Controlling mechanical sparks and friction
- Using separator devices to remove foreign materials capable of igniting combustibles from process materials
- Separating heated surfaces and systems from dusts
- Utilizing the proper type of industrial trucks
- Properly using cartridge-activated tools
- Maintaining all above equipment adequately
There are so many variables that can contribute to a dust explosion – the size of the dust particles, how they’re dispersed, the ventilation system, physical barriers and the size of work areas. Therefore, there’s no one-size-fits-all rule of thumb to measure whether you have too much accumulation or if your plant is truly at its safest.
A tailored hazard analysis is the best way to ensure your facility is as safe as possible. When it comes to the safety of your workers and the future of your business, you cannot afford to cut corners.